The Importance of Dust Collectors
Dust Collectors (also known as baghouses) are specialized equipment used in diverse industries to control air pollution by capturing and eliminating airborne dust and particulate matter produced during manufacturing, processing, or other industrial activities. These devices play a vital role in mitigating air pollution, reducing respiratory health risks for workers, and preventing damage to equipment. Despite their essential role in various industries, dust collectors are often viewed as burdensome due to their high maintenance demands, unexpected downtime, frequent valve and filter replacements, and overall limited effectiveness. However, many of these problems originate from poor diaphragm valve performance.
The MAC Pulse Valve was developed as a solution to these challenges. MAC Pulse Valves utilize a cutting-edge spool-style technology, replacing the traditional but outdated diaphragm valve technology commonly found in reverse jet dust collectors for the past six decades. These valves boast a cycle life rating that is ten times greater than that of diaphragm valves while significantly enhancing the effectiveness of each pulse. Due to their exceptional pulsing capability, MAC Pulse Valves require less frequent pulsing, necessitate reduced maintenance, consume less energy, and significantly extend the lifespan of filters. In most cases, the return on investment (ROI) for these valve upgrades is achieved in under a year.
Technology Overview
Dust Collector Upgrade Projects
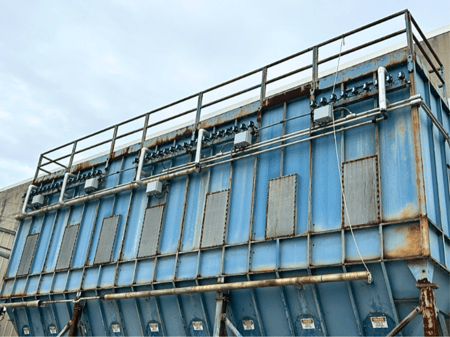
Paper Mill Reliability Driven Upgrade
A bath tissue converting line was experiencing frequent filter blinding issues resulting in four major annual shutdowns on average, causing significant production losses and maintenance challenges. The diaphragm valves on the baghouse were failing to clean the filter cartridges effectively, necessitating costly and disruptive scissor lift rentals for maintenance and changeouts.
By installing MAC's spool-style valve technology, we provided a solution that delivers a more effective pulse. This upgrade resulted in cleaner filter cartridges and significantly reduced downtime, enhancing operational efficiency and productivity.
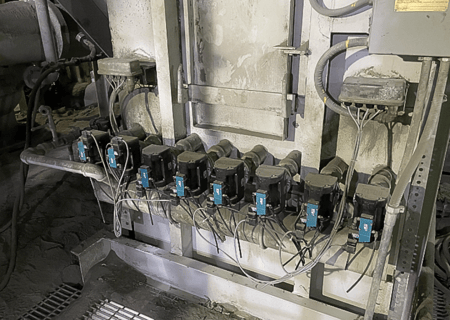
Cement Plant 8 Station Upgrade
A cement plant faced ongoing issues with diaphragm ruptures on its 8-station baghouse, leading to constant valve repairs and declining header pressure. To resolve this, we upgraded to MAC's spool valve technology, a drop-in replacement that required no piping modifications. The innovative spool design eliminated the risk of diaphragm ruptures, ensuring smoother operations and reduced maintenance.
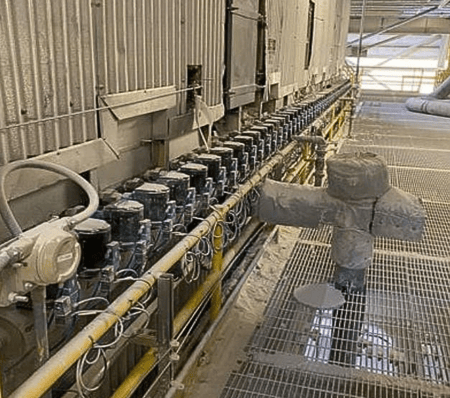
Gypsum Plant Energy Reduction Project
At a prominent gypsum plant, we upgraded 53 valves on the Impact Mill Baghouse with MAC’s innovative spool valve technology. This transformation led to a remarkable reduction in daily pulse frequency, from 700 pulses per day to just 250. The immediate impact was a dramatic 82% reduction in the annual cost of compressed air. This translated into an impressive $22,000 in energy savings within the first year alone.
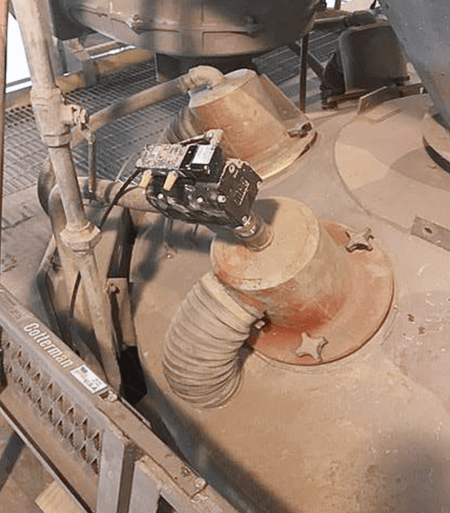
DCL Fly Ash Loading Collector Upgrade
This DCL dust collector is an integral component of a fly ash loading process. Previously, the collector utilized ASCO valves that suffered from leakage issues and were ineffective at cleaning the filter cartridges due to subpar pulsation. This forced them to remove and clean the filters every couple of weeks, causing significant disruptions to production.
To resolve these problems, we upgraded to MAC Pulse Valves, which delivered a much more efficient pulse. This improvement led to extended filter life and longer intervals between pulses, resulting in substantial air and energy savings. Additionally, we relocated the valves to the top of the collector and affixed them directly to the red "dome." This adjustment significantly improved the delivery of air pulses to the cartridges for more effective cleaning. Previously, the valves had to fill the entire hose volume before entering the dust collector, which prevented effective cleaning.
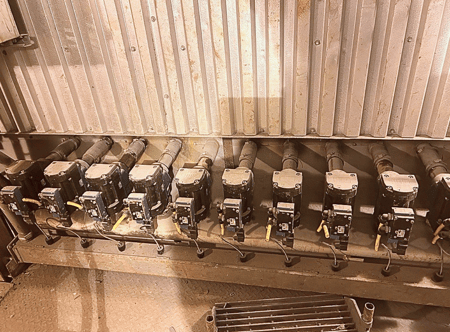
Waste-to-Energy Baghouse Upgrade
At a waste-to-energy facility, efficient dust collection is crucial for reducing air pollution and ensuring continuous operation. When faced with frequent unplanned downtimes due to inefficient filter cleaning and high differential pressure, this plant turned to MAC’s drop-in valves for a solution.
By retrofitting the dust collectors with MAC Valves, the plant significantly improved filter cleaning efficiency, eliminating the high differential pressure issue. As a result, the system now runs smoothly and reliably, ensuring uninterrupted energy production and a cleaner environment.
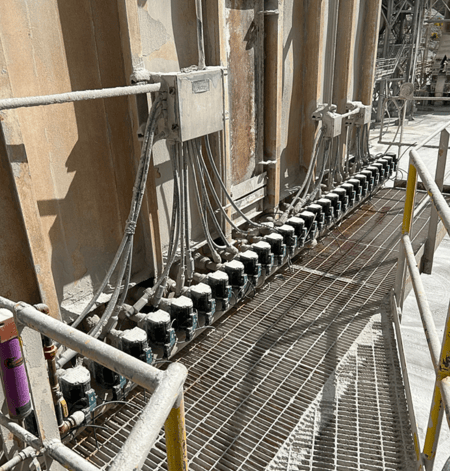
Limestone Processing Baghouse Upgrade
A limestone processing plant faced significant challenges due to high unplanned maintenance demands from their dust collectors. We introduced drop-in replacement valves from MAC to upgrade the collectors and provide relief. These new valves, with a 10x rated lifespan, transformed maintenance from an unpredictable task into a scheduled routine. Additionally, they drastically reduced compressed air demand, saving the plant an impressive $40,000 annually in energy costs.
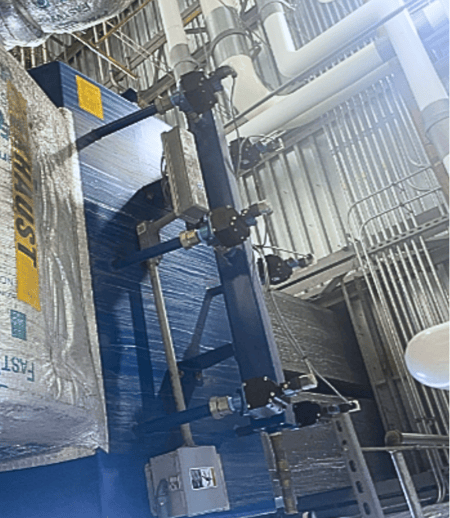
Pharmaceutical Facility Collector Upgrade
Throughout a pharmaceutical manufacturing facility, vital dust collectors purify plant air by removing material dust. To tackle energy expenditures, reduce maintenance tasks, and eliminate unplanned downtimes associated with these baghouses, we installed MAC pulse valve on smaller collectors throughout the facility. This upgrade has markedly enhanced operational efficiency, slashing maintenance and replacement part costs, while seamlessly boosting productivity and reducing energy expenditures.
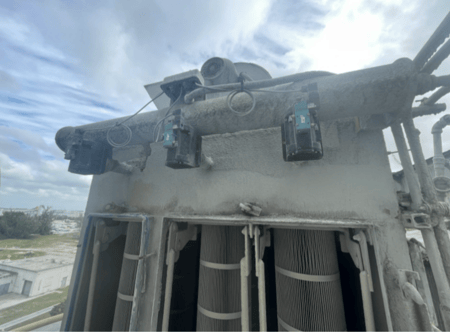
Aggregate Plant Retrofit
A dust collector atop a silo, equipped with double diaphragm Goyen pulse valves, was causing significant production issues due to high differential pressure from poor pulse effectiveness. By replacing the 1.5" Goyen valves with MAC’s drop-in replacements, we achieved a more effective pulse. This upgrade removed more material per pulse, maintained the differential pressure within the desired range, and significantly improved overall plant efficiency.