Robotic Solutions
Robotic Solutions involve to the use of robots to carry out tasks throughout the manufacturing process traditionally performed by humans. Robots are transforming the manufacturing landscape, bringing unprecedented levels of efficiency, precision, and productivity, all while freeing human workers to focus on more complex and creative tasks. By integrating advanced robotic solutions, manufacturers can streamline processes, reduce human error, and achieve consistent, high-quality output. This not only enhances competitiveness but also allows for greater flexibility and innovation in production. Embracing robotic automation is an investment in the future, enabling manufacturers to stay ahead in an increasingly dynamic and demanding market.
Common Robotic Applications
- Assembly
- Pick & Place
- Material Handling
- Machine Tending
- Screw Driving
- Dispensing
- Palletizing
- Surface Finishing
- Grinding
- Welding
- Test Stations
- Quality Inspection
- Packaging
- Kitting/Tray Loading
Robotic Applications
Cobot Machine Tending
Robotic machine tending significantly enhances manufacturing efficiency by automating the loading and unloading of machines, allowing for continuous operation without human intervention. This leads to increased production rates, reduced labor costs, and minimized downtime. Additionally, robotic machine tending improves workplace safety by handling repetitive and potentially hazardous tasks, ensuring a more consistent and reliable manufacturing process.
FANUC Stainless Steel Food-Grade Delta
The DR-3iB/6 STAINLESS is FANUC’s first stainless steel food-grade delta robot for picking and packing primary food products. Rated IP69K, the robot meets USDA and FDA food safety standards and sets a new benchmark for robotic food handling in terms of payload, speed, reach and sanitation.
The DR-3iB/6 STAINLESS features a fully enclosed stainless steel body that is resistant to the chemicals and high pressure/temperatures required in strict wash down environments found in the bakery, cosmetics, dairy, pharmaceutical and protein industries. The robot’s mirror-like surface finish ensures that any microbial contaminants can be washed away cleanly. With additional features such as NSF H1 food grade lubricant, secondary oil catch basins (with viewing windows to monitor potential leaks), self-draining surfaces, and many other small details driven by USDA/FDA standards.
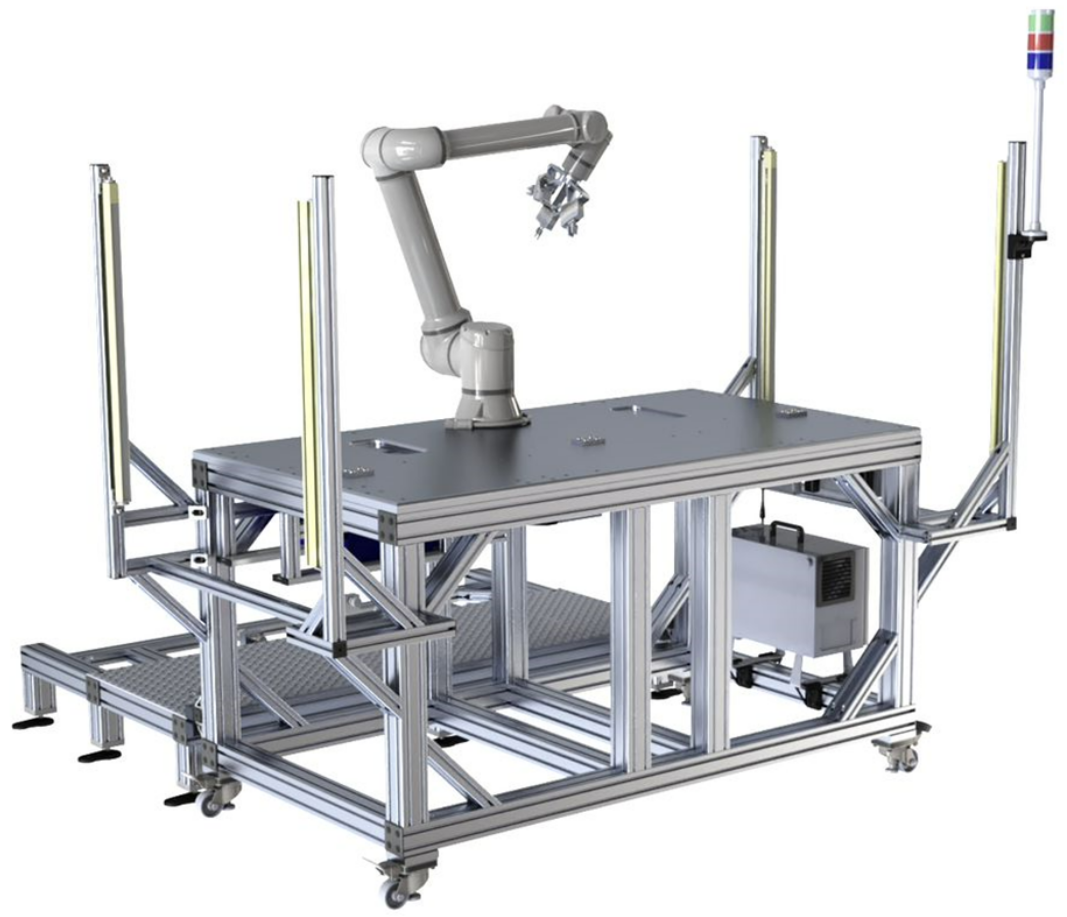
Haas Robotic Machine Tending Station
This robot cell was designed to attach directly to an existing CNC welding machine to allow for the autonomous loading and unloading of small medical parts. The project posed challenges due to the small dimensions of the parts, the stringent tolerances required, and the diverse range of parts encountered. To overcome these hurdles, our engineering team utilized a UR5e collaborative robot from Universal Robots for its size, reach, repeatability, and ease of programming.
The structure was made with 80/20 aluminum extrusion because it allowed us to customize all dimensions to meet the specific spatial requirements, as well as unique design features, such as a catwalk in between the robot table and the CNC machine, the ability to easily unhitch and move with casters, and integrated light curtains to form a protective barrier around the outer perimeter of the machine.
The protective barrier is designed to allow the operator to load parts in a safe manner while the machine is in operation. If any of the light curtains are obstructed, the robot will enter a reduced speed mode. The machine is also equipped with a safety scanner to detect operators or objects on the catwalk, in between the robot table and the CNC machine. This protective barrier is designed to allow the operator to interact with the CNC machine during calibration sequences and troubleshooting. If the scanner is obstructed, the robot will immediately stop.
Robotic Guided 3D Hole Inspection
Inspecting parts with complex geometries can often be very challenging. A customer came to us with a perplexing application that we could make a reality with a robotic guided 3D inspection system. Using a UR robotic arm with high repeatability and 3D scanners, the system can precisely position itself to scan holes from multiple angles.
The 3D scanning technology captures detailed point data throughout the hole's geometry, allowing for comprehensive and accurate dimensional analysis. This inspection method is particularly beneficial in industries where precision is crucial, such as aerospace, automotive, and medical, as it ensures that holes meet precise specifications and tolerances. By automating the inspection process, this technology significantly reduces the likelihood of human errors and increases inspection speed, thereby enhancing overall quality control and productivity.
Robotic Palletizing
Robotic palletizing offers tremendous value by automating the stacking and organizing of products onto pallets with precision and speed. This technology enhances productivity by streamlining the palletizing process, reducing manual labor and the risk of injury. It also ensures consistent and optimized stacking patterns, improving load stability and reducing shipping costs. Overall, robotic palletizing increases efficiency, lowers operational expenses, and boosts workplace safety.

Robotic Bottle Dispensing Cell
A customer faced the challenge of reconfiguring a robot work cell within a confined floor space, trying to maximize robot reach and product throughput. A crucial aspect of this cell was to efficiently organize the bottle storage area, maximizing the time between refills, as well as ensuring accessibility for an operator to replenish bottles as required. Our designed solution utilized a VT6L All-in-One 6-Axis robot from Epson, along with a new bottle storage design to reach the maximum number of bottles stored, as well the time between refills.
Cobot Welding
Robotic welding provides significant benefits by delivering precise, consistent welds with greater speed and accuracy than manual welding. This technology enhances production efficiency, reduces material waste, and ensures high-quality welds every time. Additionally, robotic welding improves worker safety by performing hazardous tasks, minimizing exposure to harmful fumes and intense heat. By integrating robotic welding, manufacturers can achieve higher throughput, lower costs, superior product quality, and allowing their skilled welders to work on more custom, higher-value tasks.
Robotic Partners
.png)
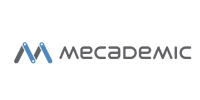