What Condition Monitoring Is and Why It Is Important
Condition Monitoring uses various sensing devices to continuously collect data regarding the condition and performance of critical assets, equipment, and processes within a manufacturing operation. This data, which includes parameters like temperature, pressure, vibration, humidity, etc. is presented in an intuitive and visually appealing format, and is accessible remotely. The data enables organizations to make informed, data-driven decisions regarding their assets. By accurately monitoring and analyzing trending asset conditions, companies can improve maintenance strategies, extend equipment lifespan, maximize uptime, and prevent unexpected downtime. Urban.io's wireless sensing devices make implementing condition monitoring easier than ever, eliminating the complexities associated with cabling and programming.
Condition Monitoring Applications
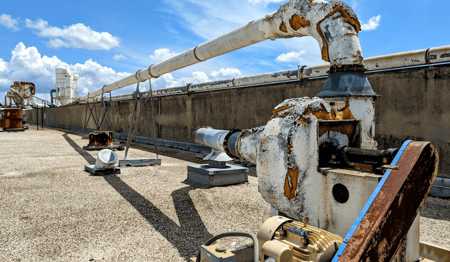
Roof-Mounted Industrial Blower
Oftentimes, equipment in hard-to-reach areas is the most neglected. In this application, a critical blower mounted on the roof is transporting material scraps. When this equipment goes down, the entire process comes to a halt, resulting in significant product loss. Therefore, we installed vibration sensors to remotely monitor the (XYZ axis) vibration of the drive end and non-drive end motor bearings, as well as the drive shaft bearings. Since these sensors communicate with the gateway via LoRa technology, no wiring was needed. This was extremely important due to the location of the equipment. They now have set vibration tolerances and can see the trends, as well as be notified if the vibration levels get near their desired set points, allowing them to address issues prior unplanned downtime events.
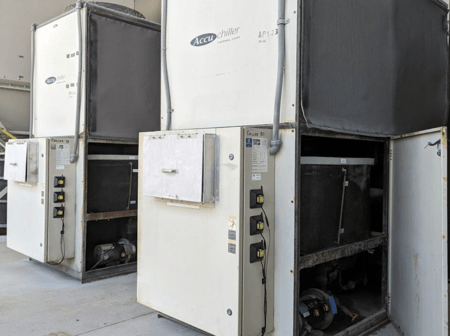
Industrial Chiller Current Monitoring
These Industrial Chillers play a vital role by facilitating the circulation of cool, clean air from the bag house to the corrugated laser cutter, preventing overheating. A malfunction in any of the chillers leads to a complete production halt. As a result, we deployed current monitoring sensors to allow for remote analysis and trending of current draw within the chiller. The customer now possesses the ability to identify potential problems before they cause unplanned downtime, allowing for strategic planning to minimize production loss impact.
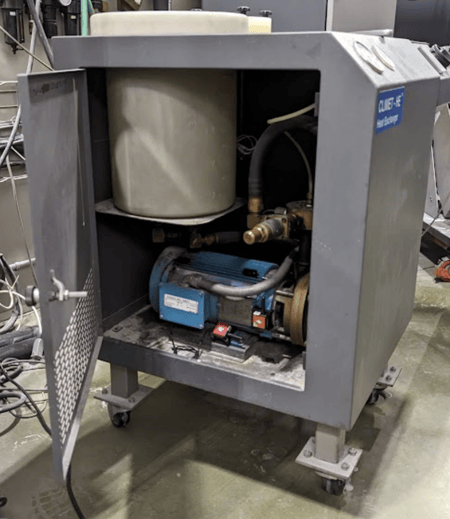
Portable Heat Exchanger Pump Monitoring
Portable heat exchangers are common in manufacturing plants but often lack the desired monitoring capabilities. With our Urban.io vibration and temperature sensors, our customer is now able to remotely monitor the relative movement and the surface temperature of the turbine water pump, which is the most critical component, as well as accurately monitor the ambient temperature inside the enclosed panel.
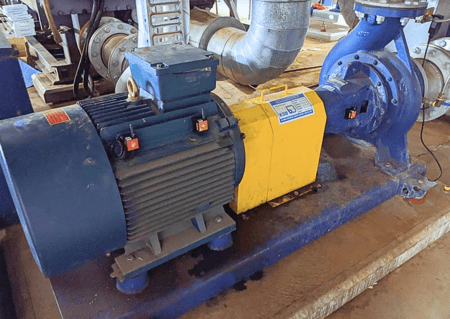
Critical Motor and Pump Monitoring
Motors and pumps are essential mechanical systems in manufacturing processes, crucial for maintaining operational efficiency. However, their often inaccessible locations can make monitoring challenging. To address this, we deployed vibration sensors and temperature probes to keep a close watch on the overall health of these critical assets. This proactive approach ensures early detection of issues, safeguarding the asset’s functionality and process reliability.
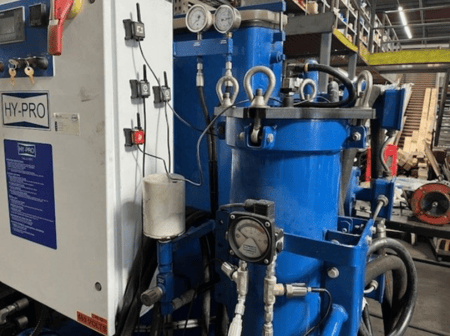
Steam Turbine Reliability Monitoring
When a steam turbine suffered from a steam seal leak and a malfunctioning water coalescer due to oil demulsibility issues, attempts at a system flush only exacerbated the problem. We intervened with a HYPRO vacuum dehydrator equipped with ICB resin to restore the compromised turbine oil. Additionally, we installed URBAN IO transmitters in just 15 minutes, allowing real-time monitoring of the leak and the effectiveness of our solution via cell phone or remote computer. This proactive approach not only resolved the oil issue but also prevented a potential summer outage, ensuring uninterrupted turbine operation.
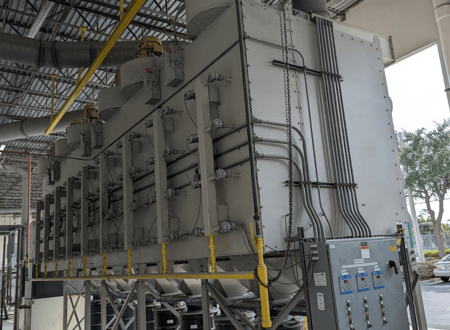
Baghouse Condition Monitoring
Dust Collectors fulfill a vital function in the manufacturing process, yet their significance is sometimes overshadowed by the recurrent maintenance challenges they present. Collaborating with a client, we undertook the enhancement of a seventy-two-valve collector through the integration of wireless differential pressure sensors, temperature probes, vibration sensors, and current monitoring sensors. The pre-existing system had its limitations; operators were required to frequently traverse the factory floor to manually engage with the equipment for real-time updates. Furthermore, the absence of trend monitoring or the means to track operator adjustments proved to be a significant shortcoming.
Following this deployment, the customer gained the ability to remotely:
- Count valve pulses.
- Monitor differential pressure across filter bags.
- Track temperatures and vibration levels of motors, fans, and belt couplings.
- Analyze the current draw of motors.