Hydraulic Filtration
Hydraulic Filtration is a process used in hydraulic systems to remove contaminants and impurities from hydraulic fluid. Hydraulic systems are widely used in various industrial industries, such as Mining, Power Generation, Paper and Pulp, Plastics, Food and Beverage, Cement, Steel, Aerospace, etc. These hydraulic systems are used to transmit power through the controlled flow of hydraulic fluid to move and control mechanical components, such as cylinders, valves, and motors. The primary purpose of hydraulic filtration is to maintain the cleanliness and integrity of the hydraulic fluid to ensure the efficient and reliable operation of the hydraulic system. Proper hydraulic filtration helps extend the life of hydraulic components, reduce maintenance costs, and enhance system performance and reliability.
Filtration Projects
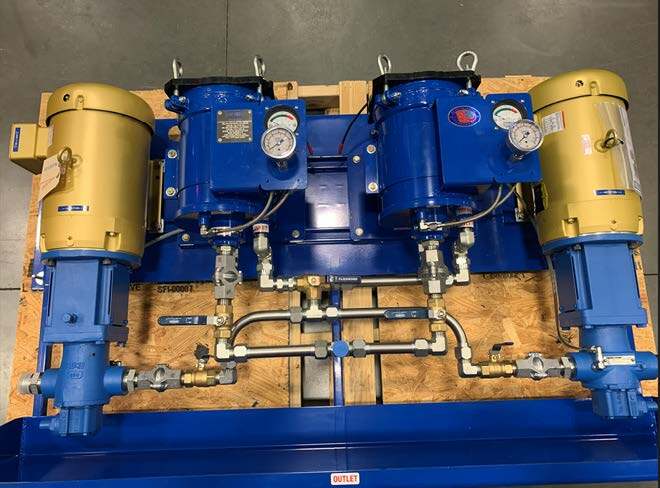
Wall-Mounted Filtration Skid for Cement Plant Raw Mill
In a cement plant, the raw mill is used to grind the raw materials into a fine powder, called raw mix, which is then fed into the kiln for further processing. The raw mill is critical to production and cannot go down unplanned.We worked with the reliability team who was having some challenges with an older gearbox filtration skid. It was a challenge to get to for maintenance, as it was located on the second floor, and was constantly requiring attention.We designed a custom filter panel that could be relocated to the first floor and wall-mounted for easy accessibility. This skid included redundant motors and pumps that would each discharge through an inline filter and could be isolated should a filter, pump or motor need to be replaced.
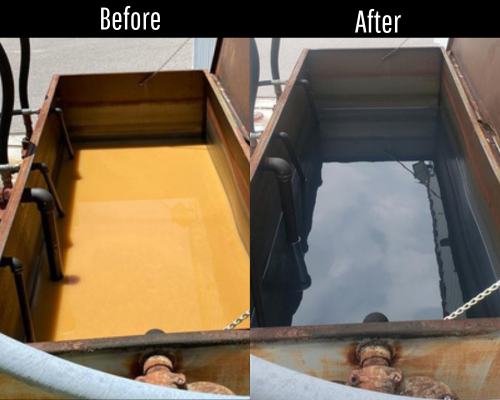
Bulk Hydraulic Fluid Water Removal
A customer had a major water issue due to a leak in the reservoir and needed to keep the system up and running. We installed a Hy-Pro Vacuum Dehydrator to remove the water quickly, as well as remove particulate contamination.
These two pictures were taken 18 hours apart! The murky oil was when the dehydrator was first installed. Our solution prevented them from buying600 gallons of new oil, having a contractor remove/replace the oil, and prevent downtime/loss of production associated with taking the unit off-line.
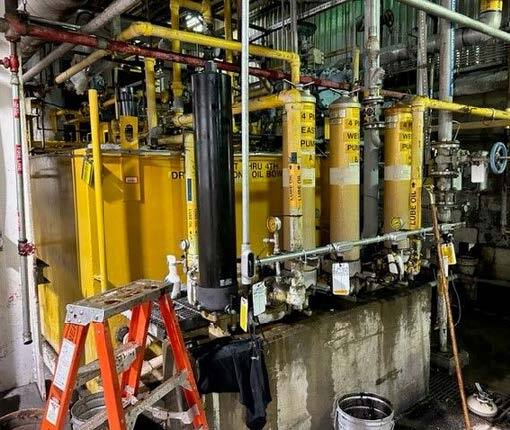
Integrated Filter Bypass
A customer from a paper mill was grappling with the challenge of regularly replacing check valves within their filter housings. If they are not changed often, they get clogged, resulting in the bypass valve sticking open, causing the dirty fluid to bypass the filter. Unfortunately, the bypass valve is often overlooked due to the time-consuming nature of replacement and pressing priorities elsewhere. To address this issue, we installed a Hy-Pro F8 filter housing, which allowed us to use the HP107 series filter element. This is significant because the HP107 element incorporates a bypass valve integrated into the filter element itself. This innovative design ensures that the bypass valve is changed every time the element is replaced. This simplifies a crucial maintenance task and guarantees that faulty check valves don't cause fluid to bypass the filter element.
Hydraulic reliability is contingent on clean fluid; any bypassing of the filter compromises this. Thanks to this solution, the paper mill's persistent bypass concerns are now eliminated.
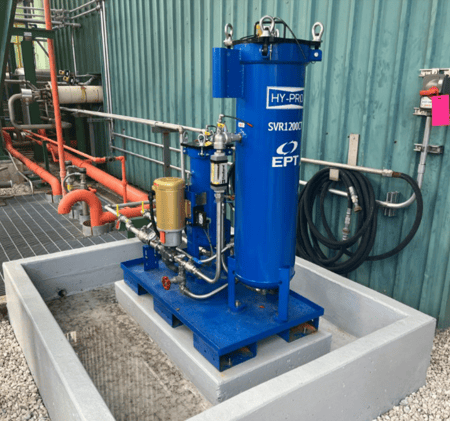
Turbine Oil Varnish Removal and Prevention
Varnish in turbine oil can severely impact the efficiency, reliability, and lifespan of the turbine system, resulting in increased maintenance costs and potential operational disruptions. To address this issue, we implemented a Hy-Pro SVR (System Varnish Removal) system. This advanced solution tackles varnish problems by purifying the oil, eliminating existing deposits, and preventing new varnish from forming. As a result, the system enhances the performance and reliability of the lubrication system, ensuring smoother and more dependable turbine operation.
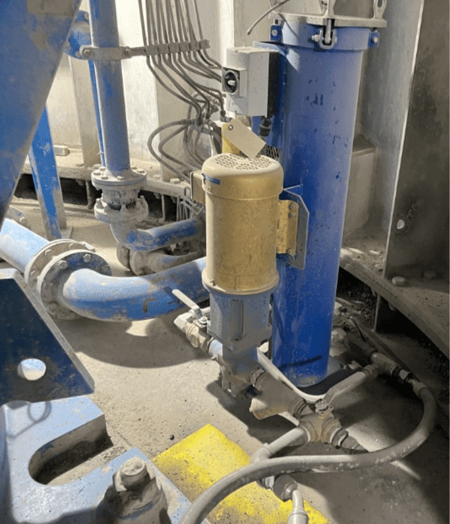
Cleaning High-Viscosity Oil
High-viscosity gear oils often lack filtration, yet rebuilding can be prohibitively expensive. At Adams, we recommend using a robust 36” filter, often filtering to 3 µm with a beta ratio of 1000. In this recent deployment, our side-stream filter, operating at 2 GPM, achieved an impressive ISO code of 15/13/10 which provided extended filter life. This approach extends the intervals between costly oil changes and rebuilds from months to years, all without interfering with high-pressure pumps.
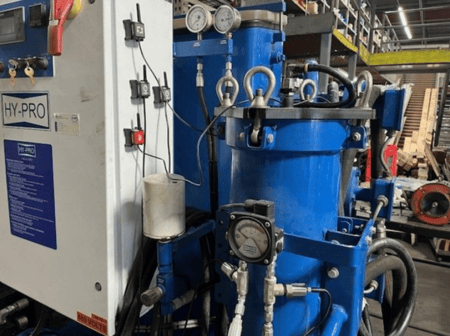
Steam Turbine Reliability
When a steam turbine suffered from a steam seal leak and a malfunctioning water coalescer due to oil demulsibility issues, attempts at a system flush only exacerbated the problem. We intervened with a HYPRO vacuum dehydrator equipped with ICB resin to restore the compromised turbine oil. Additionally, we installed URBAN IO transmitters in just 15 minutes, allowing real-time monitoring of the leak and the effectiveness of our solution via cell phone or remote computer. This proactive approach not only resolved the oil issue but also prevented a potential summer outage, ensuring uninterrupted turbine operation.