Lube Smarter and Perform Better with Automated Greasing
Lubrication plays a crucial role in manufacturing across various industries. It involves the application of lubricants to moving parts of machines and equipment, ensuring smooth operation, reducing wear and tear, and extending the lifespan of machinery. By implementing effective lubrication practices, you can prevent up to 75% of premature bearing failures. What was once a manual task, typically executed by operators using grease guns, has now been transformed by automation. Automatic lubrication guarantees precise lubricant dispensing and prevents contamination, greatly extending equipment longevity. It also improves operator safety and enables workers to concentrate on more complex and creative tasks.
Automated Lubrication Projects
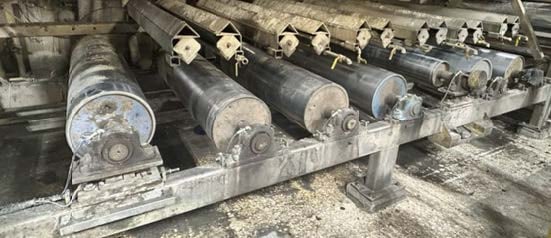
Cooling Roller Multi-Point Lubrication Project
In this critical and dirty application, a building materials manufacturer was experiencing premature bearing failure and unplanned downtime associated with their cooling rollers. We optimized the greasing process by utilizing a multi-point system to grease all bearing sevenly from a centralized, safe location. The multi-point system seals grease points and provides positive pressure in the bearings, preventing constant exposure to contamination. It also eliminated safety risks, reduced labor (swapping grease cup every 3 months vs. manually greasing daily), and significantly extended bearing life due to consistent grease dosing, which keeps the bearing in optimal lubrication range.
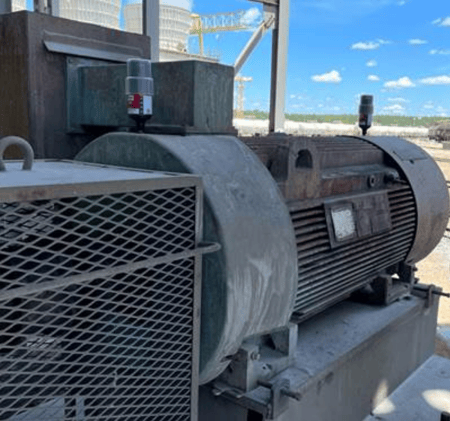
Pulp and Paper Mill Motors
Due to the large-scale layout of the facility, limited technicians, and the aim to prolong equipment life, a collaboration was initiated with a pulp and paper mill to optimize greasing practices. The objective was to shift from the conventional manual greasing approach to an automated lubrication method utilizing Perma Star Vario greasers. This transition has not only liberated the technicians to focus on more critical tasks, but also ensures that the bearings receive a steady and precise supply of grease, thus maintaining ideal lubrication conditions.
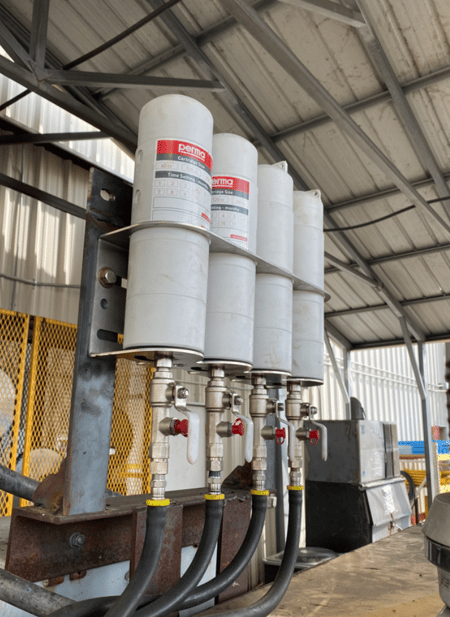
Four Station Remote Mounted Greasers
In this application, four Perma Star Vario auto greasers were strategically mounted on a heavy-duty 4-station bracket, positioned approximately 10 feet away from the grease point and shielded by a protective housing. This setup allows operators to easily change the grease cartridges and purge the lines when necessary, using the remote zerk fittings. This innovative solution ensures peak operator safety and delivers precise bearing lubrication, significantly extending bearing life.
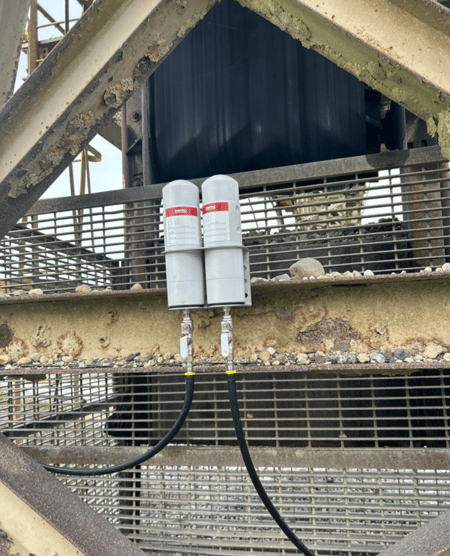
Fertilizer Manufacturer Conveyor Bearings
Large conveyors in fertilizer manufacturing facilities often span long distances and multiple levels, making them challenging to access. Ideally, relubrication should occur while the equipment is running, but this poses significant safety risks. To eliminate operator hazards and prevent equipment shutdowns, two Perma Ultra units were remotely mounted in a safe location. These units continuously grease the conveyor bearings, ensuring safety and minimizing downtime.