Varnish Remediation in a Siemens Turbine
Challenge
A municipality in Florida has a Siemens Steam turbine using 2500 gallons of Mobil DTE 846. The local maintenance staff is experiencing high particle counts and varnish levels, as high as 26.19 Membrane Patch Colorimetry (MPC) in their turbine, and the turning gear is failing to engage. In November of 2023, the municipality in Florida contacted Adams for a solution. Varnish is a result of oil breakdown from heat, pressure, and oxidation. The “broken” oil molecules are attracted to metal surfaces since oil changes do not remove the varnish. The varnish continues to build up and compromises the additives in the new oil. The varnish must be removed at temperatures above 120 degrees Fahrenheit.
Figure 1. MPC Condition Scale and MPC Ratings Before Remediation

Solution
In December 2023, Adams delivered the Hy-Pro FSTO2 and assists with setup and oil quality training. The Hy-Pro FSTO2 uses a large Resin canister with an “Ion Charged Bonding” resin that adsorbs the varnish. The oil flows slowly through this media to maximize contact time. As the varnish is removed from the oil, the older varnish begins to dissolve back into the oil from the metal surfaces. There is also a very fine particulate removal filter. Turbine manufacturers tend to use a larger micron rating, often 25 microns. By going to a 3-micron beta 4000, the ISO codes are quickly restored.
Outcome and Benefit
The Hy-Pro Filtration remediation system successfully reduces varnish MPC levels from 26.19 to 5.77 and ISO code from a 21/19/15 to a 15/14/12, as shown in Figure 3 and 4. Adams exceeds expectations on the original 90-day remediation estimate and establishes normal varnish and particle count levels in 3-weeks.
Figure 2 & 3. MPC Test Results and MPC Test Results After 6 Months

Conclusion
System flushes are extremely expensive. A typical oil change can cost upwards of $100,000 and unplanned downtime is costly as well. The removal of varnish, regardless of size or brand of turbine, increases turbine reliability and extends oil life, offering an ROI as quickly as a few months. Oil life is doubled, even tripled as additives are no longer exhausted by the varnish. In addition, the improved ISO codes can triple the life of bearings. The resin also controls acid, increases resistivity (fighting corrosion), and thus greatly extends the life of additives. Heat exchangers regain efficiency and control valves no longer stick.
Figure 4. Patch Test
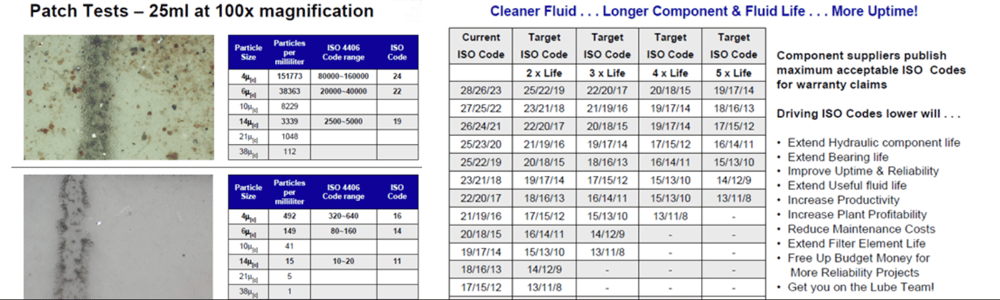
The net result is lower operating costs and higher reliability for the plant's turbines, as well as eliminated unplanned outages due to varnish buildup. Every turbine can benefit from full-time varnish control.